BMW und Daimler dabeiWie ein Leverkusener Start-up die Industrie revolutionieren will
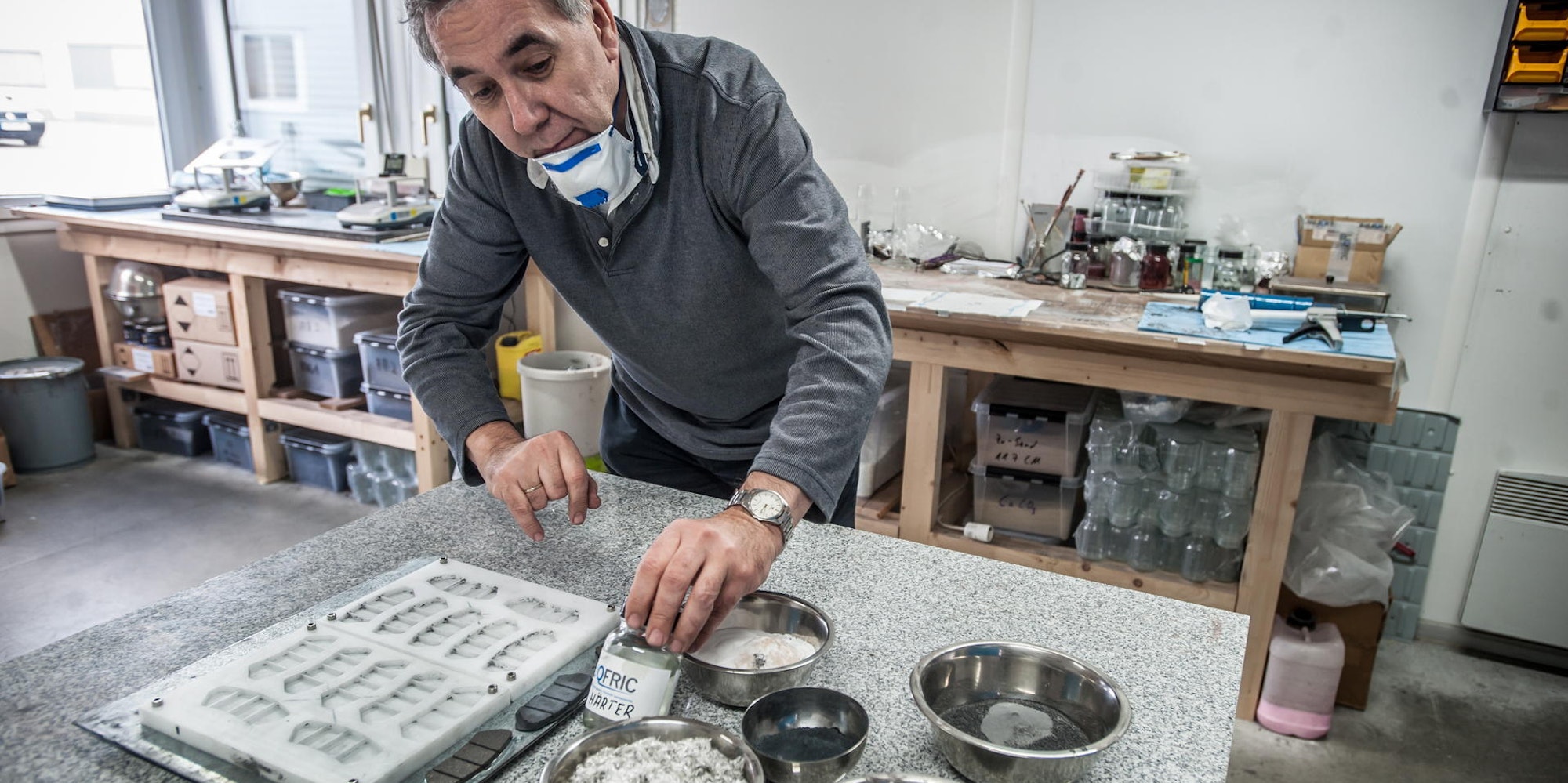
Der Chemiker Roman Milczarek mit ein paar Zutaten für Bremsbeläge auf flüssiger Basis. Nebenan die Formen für ihre Herstellung.
Copyright: Ralf Krieger
- BMW hat ein Testauto ausgerüstet, Daimler-Benz führt die Firma als Lieferanten:
- Das Start-up Liqfric macht sich auf, die Bremsbelag-Industrie in Bewegung zu bringen.
- Dahinter steht Roman Milczarek. Der Chemiker hat sein Berufsleben der Bremse gewidmet. Zuletzt leitete er bei TMD Friction die Eisenbahn-Sparte.
Leverkusen – Auf dem Markt werden jedes Jahr zehn bis zwölf Milliarden Euro umgesetzt. Und wenn es so gut weiterläuft wie bislang, wird Liqfric daran eines Tages einen nennenswerten Anteil haben. Der Kunstname steht für Liquid intelligence friction compounds und es ist damit zu rechnen, dass die Bremsbelag-Branche anders aussieht, sobald die Technologie serienreif ist.
Daran wird seit viereinhalb Jahren intensiv gearbeitet. Dazu hat Roman Milczarek ein Büro im Innovationspark Leverkusen angemietet – und eine Garage nebst Doppelcontainer in der Fixheide. Wo das Labor genau steht, will der Manager nicht so gerne verraten: Die Technologie ist spannend, das Fraunhofer-Institut begleitet das Projekt wissenschaftlich, ein Student hat die Methode zum Thema seiner Masterarbeit gemacht.
Daimler und BMW sind am Ball
Noch wichtiger: Die Industrie ist neugierig. Bei Daimler-Benz hat das Bremsbelag-Start-up aus Leverkusen eine Lieferantennummer. Das ist schon mal die Eintrittskarte ins Universum des Herstellers. Test-Ingenieure von BMW haben vor ein paar Wochen einen starken Prototyp, einen 550i, vorn mit Belägen bestückt, die ein paar Wochen zuvor in der Fixheider Miniatur-Produktion zusammengerührt wurden.
Das ist etwas völlig anderes als die herkömmliche Herstellungsmethode. Das „Backen“ von Bremsbelägen unter Einsatz der Basis Phenolharz ist praktisch seit Anbeginn der Industrie bewährt. Deshalb sei es auch gar nicht verwunderlich, dass die grundlegend andere Methode, ein Polymer in eine Form zu gießen, mit weiteren Bestandteilen anzureichern und bei höchstens 100 Grad aushärten zu lassen, nicht weiter betrachtet wurde, sagt Milczarek.
Das könnte Sie auch interessieren:
Auch bei seinem Ex-Arbeitgeber TMD Friction sei das Interesse an der alternativen Produktionsweise nicht da: Als er – naheliegenderweise – dort den Vorschlag anbrachte, eine Projektgruppe mit der weiteren Erforschung der Flüssig-Methode zu befassen, „wurde abgewunken“. So kommt es, dass nun im Schatten der früheren Textar-Fabrik am nächsten großen Ding in der Bremsen-Herstellung getüftelt wird.
Ein großes Ding deshalb , weil die Technik wegen der viel niedrigeren Temperaturen bei der Produktion rund 85 Prozent Energie einspart. Aber auch, weil es so möglich ist, Chips in die Bremsbeläge einzugießen, die den Aushärtungsprozess überstehen. „Beim Backen sind solche Teile kaputt gegangen“, erklärt Milczarek. „Die halten die Hitze einfach nicht aus.“
Ganz neue Daten
Die Piezo-Sensoren in den Test-Belägen von Liqfric aber lieferten den Ingenieuren von BMW viele Daten, als sie auf dem früheren Militärflughafen im hessischen Griesheim ihren 550i immer wieder brutal abbremsten. Die Versuche – auch sie wurden unter der Regie des Fraunhofer-Instituts gemacht – sind so wichtig, weil sie Erkenntnisse geben, „was eigentlich im Bremsbelag selbst passiert bei starker Beanspruchung“, sagt Milczarek.
Heute werde die mechanische Beanspruchung eher geschätzt, allenfalls hochgerechnet, „mit großen Sicherheitsreserven“. Mithilfe von Messergebnissen lasse sich ein Belag verkleinern – „das spart Gewicht“ an einem technisch interessanten Punkt: Rad und Bremse sind ungefederte Massen am Auto. Dass Gewichtsprobleme im Fahrzeugbau mit der Elektrifizierung nicht abnehmen, weiß man.
Mehr Abrieb? Bei E-Autos ein Vorteil
Die E-Mobilität könnte auch einen Nachteil des flüssig produzierten Bremsbelags in einen Vorteil verwandeln: Bisher sieht es so aus, als nutze sich der alternativ hergestellte schneller ab als traditionell produzierte. Weil aber Elektroautos kaum normal abgebremst werden, sondern die Energie-Rückgewinnung im Vordergrund steht, braucht man die Beläge selten. Die Folge: Die Beläge werden hart, die Bremswirkung lässt empfindlich nach. Dann, wenn sie benötigt wird. Beim flüssig hergestellten Belag „dürfte das nicht auftreten, da ist immer genug Staub drauf“, sagt Milczarek.
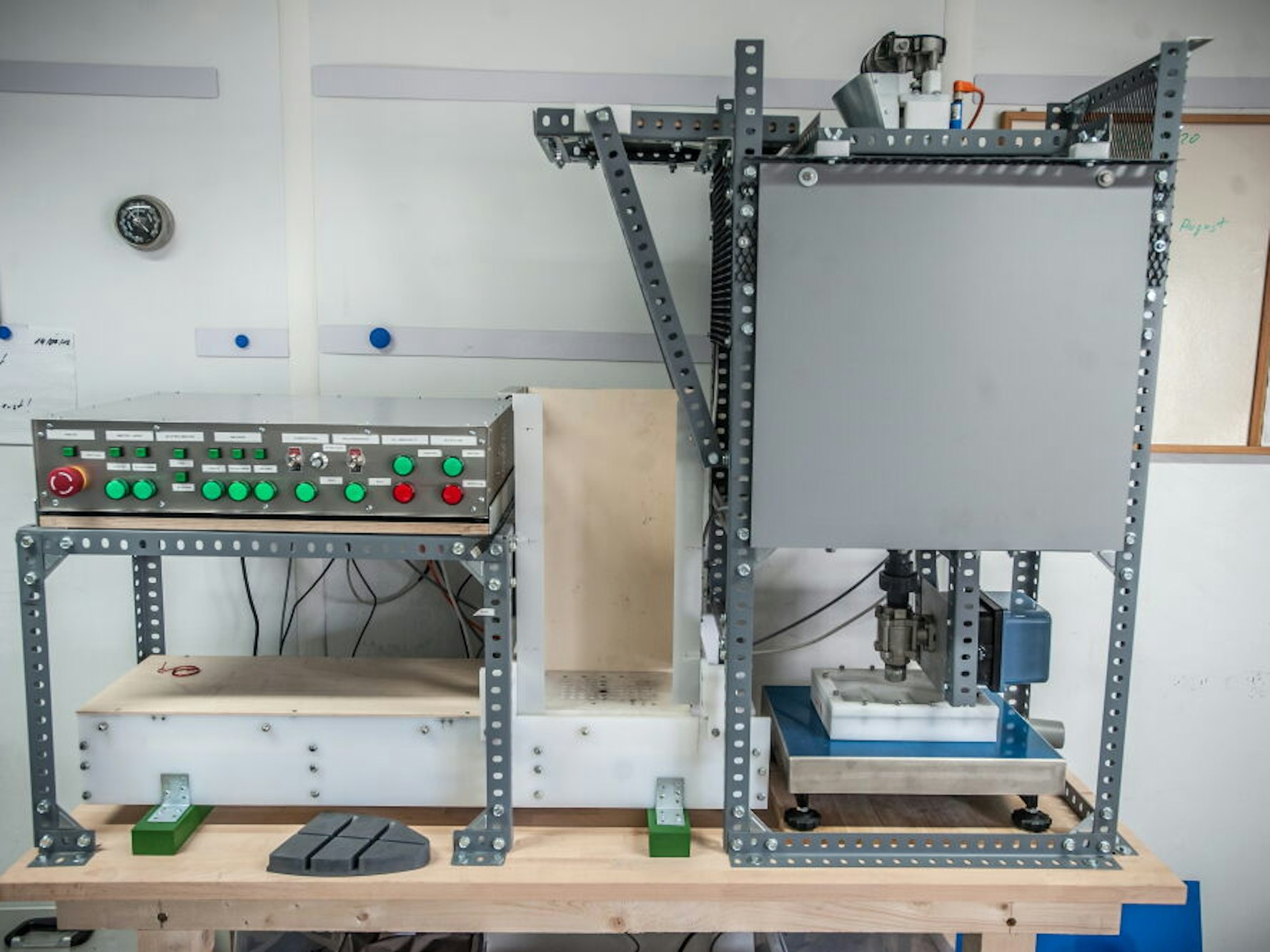
Auf dieser Anlage ist Kleinstserie für Testbeläge kein Problem. Auch Einzelstücke sind möglich.
Copyright: Ralf Krieger
Bleibt ein Punkt, der ebenfalls mit Umweltbelangen zu tun hat: Partikel der Größe PM 10 werden beim flüssig produzierten Belag kaum freigesetzt. Bremsen- und Reifenabrieb werden aber bei der kommenden Euro-7-Norm für Autos im Mittelpunkt stehen. Noch ein Grund, warum man sich in Stuttgart und München die Bremsbeläge aus Leverkusen so genau ansieht. Und warum sich Roman Milczarek Gedanken macht, wie er eine Produktion in Großserie organisieren könnte. Lizenzen für die Platzhirsche im Belagsektor, auch TMD Friction? Das wäre eine mäßig gelungene Pointe. Denn Produktion wird es in Leverkusen nicht mehr geben bei der guten, alten Textar.
Ruhestand? Nein
Sein gesamtes Berufsleben hat Roman Milczarek in der Bremsbelag-Industrie verbracht. Zuletzt war der promovierte Chemiker Chef der Sparte für Eisenbahn-Bremsbeläge bei TMD Friction. Als die verkauft wurde, unterschrieb Milczarek einen Aufhebungsvertrag. Aber für den Ruhestand fühlte er sich noch nicht reif.
Stattdessen erlag er dem Reiz jener nassen Herstellungsmethode, die zwar irgendwo in der Fachliteratur mal beschrieben, aber nie ernsthaft untersucht, geschweige denn ausprobiert wurde. (tk)
Oder doch selbst zumindest ein Werk selbst hochziehen, am besten im Chempark? „So etwas muss ich mir zumindest vorstellen können“, sagt Milczarek. Nur so kann es etwas werden mit dem Anteil am Milliardenmarkt.
Bremsen: So funktioniert das Verfahren
Gerührt, nicht gebacken. Das ist der Unterschied zur traditionellen Herstellung von Brems-, aber auch Kupplungsbelägen. Normalerweise wird ein Phenolharz mit bis zu 30 anderen Stoffen vermischt und mehrmals auf bis zu 450 Grad erhitzt. „Diese Methode gibt es seit rund 100 Jahren“, beschreibt Roman Milczarek die übliche Herstellung. „Wirklich innovativ ist die Reibbelag-Branche in den vergangenen Jahrzehnten nicht gewesen. Wenn etwas verändert wurde, geschah das auf Druck des Gesetzgebers“, sagt der Manager: Kupfer zum Beispiel sei aus den Belägen verschwunden, nachdem das in den USA verboten wurde, so der Branchenkenner.
Reaktion, nicht Aktion – das sei in der jüngeren Vergangenheit die Devise gewesen. Umso eher glaubt er, dass ein neuartiges Herstellungsverfahren Chancen hat. Denn es werde für die Autoindustrie immer schwieriger, die Umwelt-Auflagen zu erfüllen.
So könne es für die Energie-Bilanz in der Herstellung interessant sein, wenn die Produktion der Bremsbeläge in dieser Hinsicht sparsamer geschehe. (tk)